In theory, there is no difference between theory and practice. But, in practice, there is.
Johannes van de Snepscheut
Fundamental Insights
It has been said that there is no substitute for the real thing.
While that may be true when talking about your favourite recipe, the same cannot be said about developing, validating or trouble shooting industrial processes. Physical modeling offers fundamental insights into the real characteristics and performance of a system. Targeted understanding can be gained by isolating components and evaluating them in the lab with advanced methodologies and techniques.
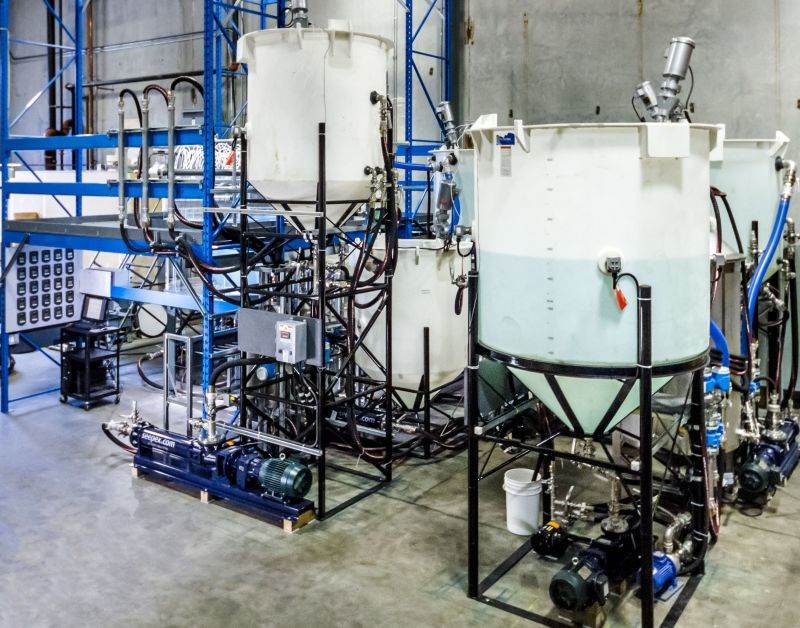
complex multiphase flow loop
A Simple Concept
In its simplest conceptual form, physical modeling is the method in which a given geometry is reproduced in the laboratory to allow the study of its performance. Most often, models are created at a different scale from the intended real-world scale, frequently at a reduced scale.
mixing reactor
pump intake model
Bypassing Technical Challenges
Many industrial processes occur under a combination of operating conditions that make it inherently difficult or impractical to directly observe, measure, or test alternative designs at full-scale conditions.
Physical modelling mitigates the road-blocks associated with attempting to study a real system. Many of these challenges occur in the following categories:
- Physical limitations
- Temperatures extremes
- Elevated pressures
- Hazardous or difficult to source materials
- Size
- Complexity
- Lack of adequate measurement techniques
- Chemical reaction issues
- Bureaucratic limitations
- Budget limits
- Timeline constraints
- Regulatory / legislative restrictions (for instance on pollution / emissions)
- Contractual obligations
- Theoretical limitations
- The system does not physically exist yet
- The technology itself does not exist yet
By building a physical scale model of the process geometry, many – if not all – of these hurdles can be addressed and eliminated. Once overcome, the process itself can then be studied leading to a better understanding of the problem and ultimately to a field-deployable solution.
Scaling
The key to effective physical modeling in the laboratory is proper scaling of the sizes, shapes and material properties to capture the important physical phenomena of the full-scale system. Often, the laboratory models are constructed at a reduced scale version of existing or proposed full-scale geometries.
Process vessels are routinely fabricated from transparent acrylic to allow for visualization and optical measurements. Alternative fluids are selected to be used in the model to match the important physical properties and flow characteristics. A combination of formal dimensional analysis and experience are used to select appropriate scales and materials.
Experience
Coanda has extensive experience in physical modeling of fluid dynamics for new process development, piloting and scale-up, commercialization, and process optimization. A properly-scaled physical model allows these topics to be investigated in a cost-effective manner and reduces the risks and potential repair, rework and trouble-shooting costs associated with poor fluid dynamic performance at commercial scales.
Physical models are a significant portion of many projects. Our in-house engineering staff, model fabrication facilities, and laboratory test facilities enable us to operate complex laboratory-scale rigs. In many cases the physical models are complemented with mathematical or computational models for a complete multi-pronged approach to the problem investigation and solutions.